Slurry Seal – Pavement Surface Treatment
Slurry seal is a cold mix paving system that can remedy a broad range of problems on streets, airfields, parking lots, and driveways. Think of Slurry Seal as an industrial-grade asphalt surfacing. The principal materials used to create slurry are aggregate, asphalt emulsion, and fillers which are mixed together according to a laboratory’s mix design formula. Water is also added for workability.
Slurry Seal Advantages
As the most versatile of any pavement surface treatment system, slurry seal is also a unique bituminous mixture that can be used to meet the demands of a variably textured surface filling cracks and voids, sealing the surface weather-tight, and providing color and texture delineation in a single pass. Some of the advantages of slurry sealing include:
- Low Cost – Slurry seal is economical to install and highly cost-effective to use. Recycled material and minimal labor save contractors and clients when opting for slurry seal application.
- Correcting & Preventing Problems – Existing distress in older pavements, surface cracking, raveling, loss of matrix, increased water and air permeability and lack of friction due to flushing or aggregate polishing can be corrected through a slurry application. Waterproofing is also achieved, preventing further deterioration. An all-weather, long-lasting surface is created that offers skid resistance and improved handling characteristics for drivers.
- Aesthetic Value – With one simple application, existing pavement receives a new wearing surface of uniform black color or texture. Enhanced appearance means increased property value, marketing potential and buyer acceptance. Thoroughfares, shopping center parking lots, and other public or commercial pavements treated with slurry seal become more attractive and eye-appealing.
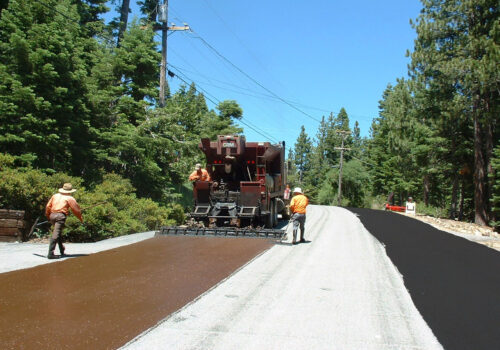
Micro Surfacing
Micro Surfacing is a mixture that is aesthetically similar to slurry seal and is applied in almost the exact same fashion. Micro can be produced utilizing either type II or type III aggregate.
- Longer Life – Micro Surfacing delivers better durability over slurry seal in that it utilizes higher quality aggregates and increased polymers in its mix designs and applications. The increase in polymers and application thickness allow micro surfacing to provide an even tougher longer-lasting surface than a slurry seal.
- Rut Filling – Due to improved chemistry of the micro surfacing emulsion, better quality aggregates and increased polymers; micro surfacing can be laid in thicker applications such as rut filling. (Rut filling is typically done with a RUT box that is specifically designed to pull the larger aggregate into the deepest part of the rut.)
- Fast Curing Time – The tough characteristics of micro and the accelerated dry time also allow micro surfacing to be opened to traffic much faster than slurry seal and is frequently placed at night minimizing impact on traffic patterns. Maximizing the opportunity to work around peak hours of traffic and business.
Chip Sealing
Chip sealing has many benefits that contractors, landowners, businesses, and municipalities look to take advantage of. Not only is chip sealing effective for protecting and repairing roadways, but it’s more affordable to implement.
- Longevity – Vehicles, weather and chemicals quickly take their toll on the roadways you traverse. Thankfully, pavement treatment methods such as chip and seal can significantly increase any road or lot’s lifespan. Sometimes, chip sealing can extend pavement life by as much as 12 years.
- Affordability – As a contractor looking to offer chip seal services, you can set lower prices when compared to other paving competitors. While the initial investment into chip seal equipment is worth considering, the material and labor used for the process are minimal and straightforward. In the long-term, your clients and business significantly save through chip and seal.
- Safety – The qualities of a chip-sealed surface offer some extra protection for drivers versus other pavement options. For example, chip-sealed pavement is skid-resistant, meaning it can reduce accidents in various weather conditions. Furthermore, chip seal surfaces are anti-glare, which reduces the eyestrain for drivers on bright or sunny days.
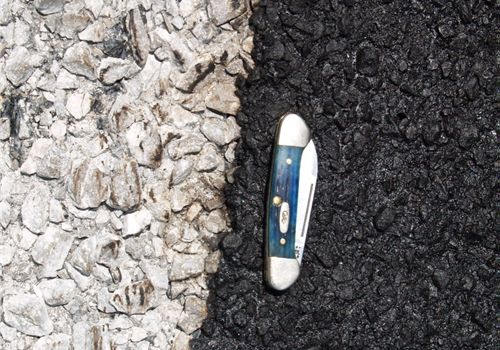
Cape Seals
Cape seal consists of a Chip seal topped with Slurry or Micro Surfacing. The cape seal can be applied to a chip seal in 24 to 72 hours. This is a multiple surface treatment that increases the life of Chip seal and makes the final product more appealing to the general public.
- Cost Effective – Cape seals are an effective combination of treatments that deliver the best of both applications listed above.
- Chip Lock – Captures and locks in the loose stones of a chip seal thereby eliminating the opportunity of vehicle damage they can cause.
- Improved Safety – Cape Seals deliver a rich black surface similar to a hot asphalt surface. When line striping/marking is applied, the black surface allows the delineation or other road marking to be easily visible to motorists.
- Water Shedding – The Cape seal helps the road to shed water due to the reduction of pockets the larger Chip seal stones provide while maintaining road friction for safety.
Making Slurry Seal or Micro Surfacing
Slurry and Micro Surfacing are made in specially designed RoadSaver II or RoadSaver IIIG mobile batch plant machines manufactured by E.D. Etnyre & Co. This equipment carries a quantity of unmixed materials that are blended together in a continuous flow pugmill. The use of this technology is made quickly and accurately at the project site. Mixing and spreading are accomplished in one continuous operation, with the surface being ready to be reopened to traffic/pedestrians within a few hours or less.
Applying Slurry or Micro Surfacing
Slurry and Micro Surfacing are applied to an existing surface by means of a spreader box linked to a RoadSaver slurry mixing unit. The blended material is introduced into the spreader box, which then lays down the Slurry or Micro coating as the mixer/spreader is driven forward.
- Spreader boxes (Augured or non-augured depending on product) are capable of applying these surface treatments over the width of a traffic lane in a single pass and are constructed so that close contact with the existing surface is maintained. This ensures uniform application of the new coating on a variety of configurations encompassing various crown shapes, super elevated, and shoulder slopes.
- Trained operators continually monitor the automatic mixing procedure. Other personnel clean the surface before slurry application, barricade and street/area, inspect the operation in progress for uniformity, clean metal utility covers after application and complete slurry seal or micro surfacing spreading in any area not accessible to the spreader box.
Contact Us